Yellow Flag Talks | La storia dei crash test in Formula 1
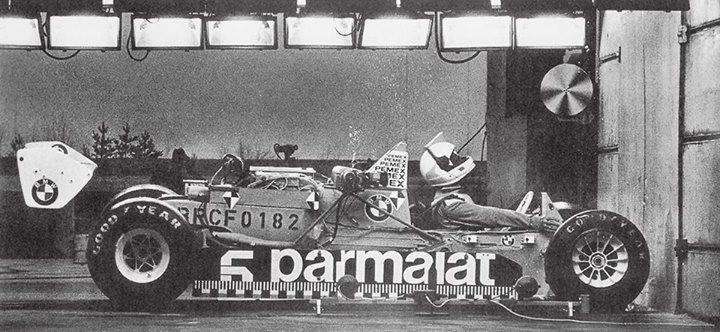
Con l’ingresso nel mese di febbraio, l’attenzione degli appassionati di F1 è interamente rivolta verso i primi riscontri in pista offerti dalle varie sessioni di test a disposizione dei team, che escono così dalla stasi invernale fatta di studi e sperimentazioni. Ma non solo.
In effetti, i primi test a cui una vettura deve sottostare non avvengono in pista, ma in specifici laboratori dove il grado di sicurezza viene messo a dura prova, sotto l’attento occhio indagatore della FIA che rilascia successivamente un certificato di conformità che, in questo 2019, sembra sia stato già ottenuto da tutte le 10 compagini partecipanti alla nuova stagione, ultime in ordine cronologico Red Bull, Ferrari e Toro Rosso.
Fallire le prove di impatto è considerata routine per squadre che puntano molto sulla sperimentazione telaistica, come la stessa Red Bull, ma per altre può rappresentare un grave inconveniente nei programmi di sviluppo: successe così per la Williams FW41 dell’anno scorso, mentre nel 2015 toccò alla versione “B” della Force India VJM08 e 3 anni prima alla Marussia MR01 che si presentò poi in Australia senza aver ancora saggiato la pista. Si può tornare ancora più indietro nel tempo, ma mai oltre il 1985. E il motivo è semplice: fu in quell’anno che il termine “crash test” fece la sua prima comparsa nel regolamento tecnico della F1.
Una lenta evoluzione
Non si può non sorridere al pensiero che quelle primitive prove d’impatto si limitassero ad un esaustivo “lancio” del telaio contro un muretto, senza particolari criteri da rispettare, ma è da considerarsi pur sempre un passo avanti dato che fino all’anno prima erano i costruttori ad auto-certificare la resistenza delle principali strutture poste a protezione del pilota: considerato “P” il peso della vettura in ordine di marcia, il musetto doveva sopportare 25P senza che la pedaliera arretrasse oltre i 15 cm (norma istituita nel 1978), mentre il roll-bar 1,5P lateralmente, 5,5P longitudinalmente e 7,5P verticalmente (norma del 1969).
La nascita dei moderni crash test può essere fatta coincidere con le annate 1991-1992, con tutta probabilità a seguito del tremendo incidente di Donnelly a Jerez nel 1990
e quello meno cruento ma altrettanto incredibile di Martini a Imola lo stesso anno,
in cui osservando le monoscocche sbriciolate della Lotus e della Minardi fu chiaro che i team di F1 alleggerivano esageratamente i telai da usare in pista. Vengono regolamentate le prove di impatto frontale, istituite quelle relative al roll-bar e incrementato il numero di prove con carico statico, introdotte per la prima volta nel 1988. Nel descrivere queste 3 premettiamo che, d’ora in poi, le unità di misura originali saranno convertite a quelle maggiormente note per motivi di fruibilità della trattazione:
- carico di 2040 kg esercitato per un minimo di 30 secondi sul fianco della cellula di sopravvivenza in 3 punti differenti (zona pedaliera, torso del pilota e serbatoio) con deformazioni permanenti non eccedenti 1 mm.
- carico di 3060 kg esercitato per 30 secondi sul lato del musetto, senza che questo si stacchi dal telaio.
- carico di 1275 kg esercitato per 30 secondi sotto la cellula di sopravvivenza, in corrispondenza del serbatoio, con deformazioni permanenti non oltre 0.5 mm.
La struttura per il ribaltamento, come detto, deve resistere ad una prova con carico combinato di 1170 kg laterali, 4290 kg longitudinali e 5850 kg verticali, sia per quanto riguarda il roll-bar dietro il casco del pilota, sia quello posto di fronte all’abitacolo con il quale si traccia la linea sotto cui deve stare il casco del pilota per garantire la massima sicurezza in caso di cappottamento.
Per quanto riguarda il crash test frontale, la monoscocca con manichino di 75 kg a bordo e serbatoio riempito d’acqua viene lanciata contro una barriera a 40 km/h. Nell’impatto, la decelerazione di picco non deve superare i 60G per più di 0.003 secondi e non deve provocare danni a cinture ed estintori.
Nel 1994 il carico statico laterale viene portato a 2550 kg, ma sono cifre destinate a salire proprio a seguito di quella drammatica stagione: dal 1995 la velocità nei crash test frontali passa a 43 km/h e i danni devono riguardare esclusivamente la struttura d’assorbimento d’urto senza intaccare la parte di monoscocca davanti i piedi del pilota (aumentata da 15 a 30 cm). Il musetto inoltre deve sottostare ora ad un carico statico di 4080 kg, ma soprattutto vengono dimensionate le strutture d’assorbimento laterale che devono reggere l’impatto con una massa di 780 kg lanciata a 25 km/h senza trasmettere alla scocca una decelerazione superiore i 10G.
Nel 1996 vengono innalzate le pareti della scocca, in modo da proteggere maggiormente la testa del pilota, e i bordi dell’abitacolo vanno testati su entrambi i lati con un carico statico di 1020 kg per 30 secondi con deformazioni permanenti non oltre 1 mm.
Nel 1997 vengono introdotti i crash test posteriori, con la struttura d’assorbimento imbullonata alla scatola del cambio che deve sopportare l’impatto con una massa di 780 kg lanciata a 43 km/h generando una decelerazione media non superiore ai 35G.
Il 1999 vede una variazione dei parametri per quanto riguarda il crash test frontale, con velocità che passa a 47 km/h e decelerazione media non superiore ai 40G (mentre nei primi 150 mm di deformazione del muso non deve superare i 5G). In più viene istituita una prova d’impatto sul sistema di sterzo, che deve essere progettato per collassare se una massa di 8 kg lanciata a 25 km/h subisce una decelerazione superiore a 80G nel contatto. In più il meccanismo di sgancio del volante deve rimanere funzionante.
Ormai le procedure sono collaudate, e passando attraverso gli anni ’00 le uniche variazioni riguardano l’innalzamento degli standard di resistenza, l’introduzione di nuove prove statiche e il test dei pannelli anti intrusione in kevlar e successivamente in zylon, fino ad arrivare all’attuale normativa.
A quali prove deve sottostare una monoposto di F1 nel 2019?
Un’attuale vettura da F1 deve sottostare a 13 prove con carico statico, rigidamente normate dall’articolo 18 del regolamento tecnico in vigore, prima di procedere con gli effettivi crash test dinamici:
- 2 test sui fianchi della cellula di sopravvivenza, rispettivamente di 2550 e 3061 kg per 30 secondi minimi con deformazione massima di 1 mm.
- 1 test sul fondo della scocca in corrispondenza del serbatoio con 1275 kg per 30 secondi minimi e deformazione massima di 0.5 mm.
- 1 test sul fondo della scocca in corrispondenza dell’abitacolo con 1530 kg per 30 secondi minimi e deformazione massima di 0.5 mm.
- 2 test su punti diversi del bordo dell’abitacolo con 5102 kg per 30 secondi minimi e deformazione massima di 1 mm.
- 2 test sull’ancoraggio del musetto, con quest’ultimo fissato prima su un piano apposito e poi direttamente alla scocca, e soggetto in entrambi i casi a carichi laterali di 3571 kg per 30 secondi senza che la struttura si stacchi.
- 1 test sui pannelli anti intrusione posti sul fianco della cellula di sopravvivenza, soggetti ad una prova di penetrazione tramite cono rigido spinto ad una velocità di 1-2 mm/s, con avanzamento massimo di 150 mm, e carico che a 100 mm deve essere di 25493 kg con un assorbimento di energia di 6000 J senza che la struttura ceda.
- 1 test sulla struttura d’assorbimento posteriore, caricata con 4082 kg laterali per 30 secondi minimi senza che questa si stacchi.
- test sull’ancoraggio delle due strutture d’assorbimento laterali, di cui:
- quella superiore caricata con 4082 kg verso il retro e il fronte della vettura, 2755 kg verso il basso e 10204 kg verso l’interno.
- quella inferiore viene caricata con 6122 kg verso il retro e il muso della vettura, 3571 kg verso l’alto e 15306 kg verso l’interno.
In tutti i casi i componenti in carbonio non devono staccarsi dal loro attacco sul fianco della scocca, né compromettere la resistenza di quest’ultima.
Successivamente vengono condotte le prove d’impatto vere e proprie, trattate nell’articolo 16 del suddetto regolamento tecnico, a partire da quella frontale divisa in due test: nel primo caso, la monoscocca viene assicurata ad un carrello (peso totale di 780 kg) spinto contro una barriera alla velocità di 54 km/h con decelerazione massima di 10G entro 100 mm, di 20G tra 100 e 150 mm, e picco non superiore a 45G. Nel secondo test, una piastra di alluminio spessa 50 mm viene fissata al posto del musetto e la monoscocca così equipaggiata viene fatta impattare a 54 km/h contro una barriera dotata di 6 protuberanze calibrate. La decelerazione sul manichino posto nell’abitacolo viene annotata, così come la resistenza di cinture e impianto d’estinzione.
Per quanto riguarda la struttura d’assorbimento posteriore, questa viene compressa da un peso di 780 kg lanciato a 40 km/h restituendo una decelerazione massima di 20G per un tempo non superiore ai 0.015 secondi.
Nessuna sostanziale differenza riguarda la prova d’impatto col sistema di sterzo, mentre roll-bar principale e secondario sono stati via via irrobustiti per far fronte a crash test sempre più severi, come si può intuire dal fatto che gli sia stato dedicato un articolo apposito, il 17 del regolamento tecnico: la struttura principale alle spalle del pilota viene gravata con 5099 kg laterali, 6118 kg longitudinali e 9177 kg verticali per un tempo minimo di 10 secondi e la deformazione ammessa è di 25 mm sull’asse del carico e 100 mm in senso verticale, mentre la struttura secondaria deve sopportare prima 11828 kg verticali e 4690 kg longitudinali e successivamente 9483 kg laterali e 8464 kg longitudinali, in entrambi i casi per minimo 5 secondi senza accusare cedimenti.
Barriere, caschi e Halo: crash test dilaganti
Il potenziale delle prove d’impatto non si limita alle vetture, ma può restituire riscontri fisici, meccanici e biomedici importanti per valutare altre strutture direttamente connesse al problema della sicurezza. Del resto, che progresso avremmo se ci fossero ancora muretti incapaci di dissipare l’energia di un urto, o protezioni per la testa utili solo a ripararsi dal vento? La sicurezza ha fatto passi da gigante anche in questi aspetti, grazie alla FIA e ai suoi collaboratori esterni.
Le barriere, ad esempio, hanno subito un’evoluzione dopo l’incidente in cui Michael Schumacher si ruppe una gamba nel 1999 a Silverstone. La FIA, insieme all’istituto di sicurezza stradale tedesco DEKRA, ha messo in cantiere la realizzazione di barriere ad assorbimento d’energia, trovando nella ditta francese TecPro il partner ideale: le strutture proposte hanno un peso nominale di 140 kg, sono composte da contenitori plastici contenenti 60 cm di polietilene e un’anima d’acciaio dello spessore di 2 mm, tenute insieme da nastri di nylon per formare una linea continua da porre all’esterno delle curve.
Appositi carrelli muniti di musetto da F1 vengono utilizzati sin dai primi anni ’00 per testare le capacità di assorbimento e protezione di queste barriere, a velocità crescenti, fino ad arrivare all’attuale configurazione (TecPro – 6 strati di gomme intervallati da polietilene – guardrail) che ha dimostrato di ridurre del 40% l’energia sprigionata in un impatto a 218 km/h. Non a caso questa soluzione è stata premiata nel 2006 come “Safety Innovation of the Year”, trovando impiego già da quell’anno a Monza (seppur i primi utilizzi si possono riscontrare al Paul Ricard nel 2005) e la sua utilità è tuttora evidente: è grazie alle barriere TecPro se Carlos Sainz Jr. ha sperimentato una decelerazione di soli 42G schiantandosi a 153 km/h nel 2015 a Sochi, incidente che ha richiesto ulteriori accertamenti e prove d’impatto per capire come mai la Toro Rosso del pilota spagnolo si sia infilata al di sotto dei pesanti cassoni plastici. Segno di un’organizzazione sempre attenta a capire e prevenire dinamiche pericolose, che in quell’episodio ha trovato la causa nel rimbalzo operato dal guardrail posto in fondo alle barriere.
Certo, il giovane Carlos Sainz ha potuto beneficiare anche della protezione offerta dal suo casco, altro oggetto sottoposto a severi test e rigide omologazioni. Risale al 1977 la norma che riservava alla Federazione l’approvazione o meno del casco di un pilota, mentre nel 1994 gli standard qualitativi diventano 3 e più stringenti (Snell/BSI/SFI), seppur con caschi ancora molto grezzi e pesanti.
Nel 2004 la direttiva FIA 8860-2004 ha imposto nuovi vincoli ai 3 principali produttori di caschi, Arai, Bell e Schuberth, che hanno modificato conseguentemente struttura e realizzazione dei loro prodotti: i caschi vengono sagomati scansionando le fattezze del pilota, e costituiti successivamente da circa 120 strati di carbonio, aramide ignifuga e kevlar, più rinforzi in alluminio e titanio, con imbottitura interna in Nomex e visiera di 3 mm in policarbonato. Così concepito, un casco arriva a pesare poco più di 1 kg (con grande sollievo del collo dei piloti, soggetto a forze paurose in curva e staccata) e, soprattutto, risulta praticamente impenetrabile come dimostrano gli appositi crash test:
- caduta di un peso di 3 kg da 3 metri d’altezza senza riscontrare danni.
- pressione di 38 kg con allungamento massimo del cinturino di 3 mm.
- visiera colpita da proiettili sparati a 500 km/h con penetrazione massima di 2,5 mm.
- esposizione a fiamma di 800°C per 45 secondi, con temperatura interna che non deve superare i 70°C.
Nel 2011 si passa ad una prova di carico di 55 tonnellate senza deformazioni, più l’aggiunta di uno strato di 50 mm di Zylon nella parte alta della visiera, per aumentare la resistenza in quest’area dopo la terribile esperienza di Felipe Massa in Ungheria nel 2009, mentre nel 2018 viene presentato il nuovo standard in vigore dall’anno successivo: i caschi, profondamente rimodellati e costruiti con nuovi materiali, devono superare test ancora più severi elencati nella tabella sottostante.
Rimanendo sul tema della protezione del capo del pilota, sono sicuramente più recenti i crash test per valutare l’adozione di strutture capaci di deviare detriti indirizzati verso il casco. Questi sono stati condotti parallelamente a prove specifiche per valutare la facilità con cui i moderni musetti da F1 possono causare decolli o schiacciamenti della vettura sotto un’altra nel caso di impatto ad alta differenza di velocità. Tuttavia il grosso degli sforzi si è concentrato sui primi: il 25 e 26 maggio 2011 al Bentwaters Airfield di Ipswich, Inghilterra, sono stati messi a dura prova diversi dispositivi tramite l’impiego di un cannone ad azoto compresso (circa 83 bar) capace di scagliare una ruota di 20 kg a 225 km/h. Sono stati testati parabrezza in policarbonato, roll-bar in titanio, cupolini aeronautici e l’Halo, introdotto poi nel 2018 aprendo un vero e proprio dibattito.
Proprio questo malcontento su un dispositivo giudicato anti estetico, più i tanti dubbi su effettiva utilità e ostacolo al pilota in fase di estrazione dall’abitacolo lasciano aperta la porta ad altre soluzioni che richiederanno altre prove, altri studi, e altro impegno di tecnici e ingegneri, da decenni in prima linea per analizzare dinamiche fisiche, meccaniche e mediche all’origine del ferimento di piloti, con risultati notevoli come l’HANS che sarà oggetto di approfondimenti nelle prossime settimane.